Your Shopping Cart
By using this site you agree to our use of cookies. Please refer to our privacy policy for more information. Close
Home
› Best Practices
Best Practices for Maintaining Device Master Records (DMR) for Medical Devices
- By: Staff Editor
- Date: September 30, 2011
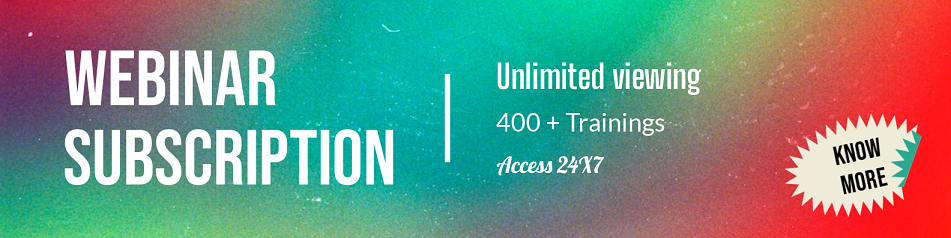
The Food and Drug Administration (FDA) requires manufacturers of medical devices to create and maintain a device master record (DMR). Section 820.3(j) of the Federal Code defines device master record. DMR is a set of documents containing procedures and specifications for a finished medical device. Simply put, device master record (DMR)is acollection of all the documents required to manufacture and test a medical device.
The need to maintain DMR
DMR is a part of the Quality System Regulation (QSR) of FDA to maintain standards in the manufacture and maintenance of medical equipment. It ensures the safety of the end-users, namely, patients. It is mandatory for a manufacturer to maintain DMR. The DMR is prepared and approved in accordance with section 820.40.
Preparation and approval of DMR’s
Each manufacturer should maintain device master records (DMR’s). The manufacturer should ensure that each DMR is prepared and approved as prescribed in Sec. 820.40. The DMR for each type of device should include or refer to the location of the following:
- Specifications of the device including appropriate drawings, composition, formulation, component specifications, and software specifications.
- Details about production methods including appropriate equipment specifications, production procedure, and production environment specifications.
- All the quality assurance criteria, procedures, and specifications. It also includes the criteria and equipment used to check quality.
- Specifications for packaging and labeling with details of methods and processes.
- Procedures and methods for installation, maintenance, and servicing.
Device Specifications the DMR should show:
The device specifications that the DMR should furnish are given in the following Table:
Name of the
Product
|
Performance
Characteristics
|
Classification
|
Physical
Characteristics
|
Environmental
Limitations
|
Important
Components
|
User Safety and
Performance
Considerations
|
|
|
|
|
|
|
|
Outline of best practices in DMR
At present regulations in the medical device industry are coming under high scrutiny with product recalls. Research continues to enhance levels of consumer safety. The proactive regulatory bodies are responding with meetings on notifications for markets before commencement of production. Investments in medical device safety are increasing. Leading providers of global quality and compliance management systems recommend that companies act together to get devices quickly to the market. Companies also need to see that devices are compliant with regulations, both current and future ones. The recommended best practices are:
- Managing quality of suppliers: Give priority to global suppliers who offer the highest quality and track them consistently.
- Electronic medical device reporting (eMDR): Create a single simplified system to maintain and manage the reports.
- Managing change: Whenever there is a change in the process, strict controls and tracking is to be done.
- Handling complaints: Recording and tracking of all complaints is to be done regularly. The authorities are to be notified regarding the number and the type of such complaints.
- Corrective and preventative action (CAPA) management: Get to the source of the problem, do the needful corrections, and see that they do not happen again.
Need to gain a better understanding of complying with regulatory requirements for medical device DMR? Attend any of the following ComplianceOnline webinars:
|
||
Many industry players suggest that every company document its DMR policy. This will result in product consistency, document organization, and easy reference. Today, several automated solutions are available to help companies organize, maintain, and communicate about device master record (DMR), design history file (DHF) and bill of materials (BOM)—and succeed with reduced manpower in a competitive and highly regulated environment. The following Table explains how automated solutions score over the manual system.
Manual system
|
Automated solution
|
Product changes documented manually resulting in errors and delay
|
Automation ensures accuracy and speed.
|
Multiple bills of material and records in various departments
|
The solution maintains one version centrally
|
Manual quality monitoring and auditing result in high overheads
|
Automatic monitoring of quality reduces labor costs.
|
Use of different sources like internet, phone, and fax for data exchange prevents effective collaboration
|
Collaboration is made easier for the team.
|
Regulations, which change often, lead to duplication of data and requires time and personnel
|
Duplication is eliminated by using the solution
|
Maintaining large amount of data physically in files is difficult
|
The solution easily manages any amount of data
|
Conclusion
Since patient safety is of paramount importance, manufacturers of medical devices should adhere to best practices, duly supported by automated solutions. This will help them to comply with the changing regulatory requirements effortlessly.
Sources:
- http://www.fda.gov/MedicalDevices/DeviceRegulationandGuidance/PostmarketRequirements/QualitySystemsRegulations/MedicalDeviceQualitySystemsManual/ucm122576.htm
- http://www.product-lifecycle-management.com/21cfr820-m-181.htm
- http://www.prnewswire.com/news-releases/regulatory-compliance-five-best-practices-for-medical-device-manufacturers-84696112.html
- http://tech-clarity.com/clarityonplm/tag/equipment-service-management/
- http://www.qualitycoach.net/land/toc/ISO13485SampleProcedures.pdf
- http://www.cmdcsystems.com/advdmr.htm
- http://www.arenasolutions.com/resources/whitepapers/dl/device-master-record.html
Compliance Trainings

Pregnancy in the Workplace: Strategies to Protect Your Organization from Pregnancy Discrimination Claims
By - Christopher W. Olmsted
On Demand Access Anytime
By - Christopher W. Olmsted
On Demand Access Anytime

How to Vet an IRB: Expose and Fix Problems Before They Threaten Your Trial
By - Madhavi Diwanji
On Demand Access Anytime
By - Madhavi Diwanji
On Demand Access Anytime

Compliance Standards
Best Sellers
- Add to Cart
- Add to Cart
- Add to Cart
- Add to Cart
- Add to Cart
- Add to Cart
- Add to Cart
- Add to Cart
-
By: Miles HutchinsonAdd to CartPrice: $249
- Add to Cart
- Add to Cart
- Add to Cart
- Add to Cart
- Add to Cart
- Add to Cart
-
San Francisco, CA | Aug 6-7, 2020
-
Virtual Seminar | Jul 16-17, 2020
-
Virtual Seminar | Jun 18-19, 2020
-
Los Angeles, CA | Aug 20-21, 2020
-
Virtual Seminar | Jul 16-17, 2020
-
Virtual Seminar | Jun 25-26, 2020
-
Virtual Seminar | Jun 10, 2020
-
Virtual Seminar | Jun 3-4, 2020
-
Virtual Seminar | Jul 6-7, 2020
-
San Francisco, CA | Oct 22-23, 2020
-
Virtual Seminar | Jul 9-10, 2020
-
Virtual Seminar | Jun 3-4, 2020
-
Virtual Seminar | June 3-4, 2020
-
Miami, FL | Jul 29-31, 2020
-
Virtual Seminar | Jun 17, 2020
-
Provider: ANSIAdd to CartPrice: $142
- Add to Cart
- Add to Cart
- Add to Cart
-
Provider: ANSIAdd to CartPrice: $120
-
Provider: ANSIAdd to CartPrice: $250
-
Provider: SEPTAdd to CartPrice: $299
- Add to Cart
-
Provider: Quality-Control-PlanAdd to CartPrice: $37
- Add to Cart
-
Provider: At-PQCAdd to CartPrice: $397
- Add to Cart
- Add to Cart
- Add to Cart
- Add to Cart
You Recently Viewed
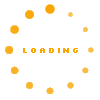