Your Shopping Cart
By using this site you agree to our use of cookies. Please refer to our privacy policy for more information. Close
Home
› Best Practices
Cleanroom Restart Procedures after Worst-Case Events
- By: Staff Editor
- Date: August 02, 2018
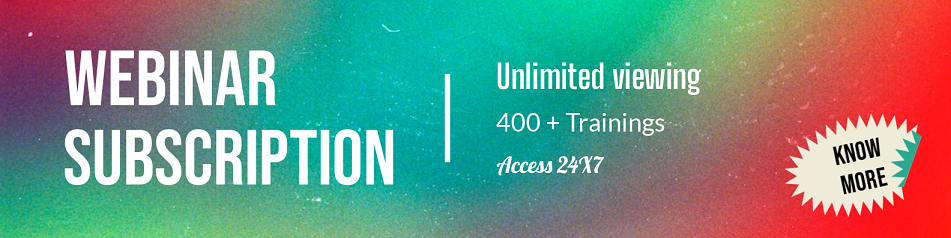
Cleanroom Restart Procedures after Worst-Case Events
Unexpected things happen everywhere. Cleanrooms are no exceptions for such. Worst-case events like bad weather conditions, power outage, airflow suspension, or serious excursions during environmental monitoring (EM) can occur. They are unavoidable and might require a temporary major or minor shutdown of the cleanroom.
Restarting to meet the acceptable standards
It is important to restore the cleanroom to the acceptable standards to prevent significant gaps in quality control. Many firms have received warning letters during inspections and have faced rejections because they failed to restore the cleanroom to the acceptable standards.
Cleanroom restart after the shutdown is a critical operation. Returning to production after the shutdown requires certain cleaning and environmental verification steps. Each facility must consider all aspects of shutdown that could affect the operation and develop detailed standard operating procedures for each aspect to guide staff.
Worst case scenario #1 Major shut down: Restart procedure:
- Clean walls, ceilings, doors and window panels by mopping with purified waters and detergents.
- Make sure that the air handling units are in operation
- Purge the area for at least one hour
- Re-Clean and disinfect the area ensuring that the floors, doors, and window panels are cleaned and disinfected.*
- Clean all equipment thoroughly internally and externally
- Perform microbial environmental monitoring
- Perform non-viable counts in the area and all the rooms
- Perform testing operations after achieving the suitable environmental conditions for viable and non-viable* counts.
- Ensure approvals by Quality Assurance
Worst case scenario #2 Minor shut down: Restart procedure:
- Make sure that the air handling units are in operation
- Purge the area for at least one hour
- Clean and disinfect the area ensuring that the floors, doors, and window panels are cleaned and disinfected.
- Clean all equipment thoroughly internally and externally
- Perform microbial environmental monitoring
- Perform non-viable counts in the area and all the rooms
- Perform testing operations after achieving the suitable environmental conditions for viable and non-viable counts
- Ensure approvals by Quality Assurance
Worst case scenario #3 Interruptions: Restart procedure:
- Make sure that the air handling units are in operation
- Clean and disinfect the area ensuring that the floors, doors, and window panels are cleaned and disinfected.
- Perform microbial environmental monitoring
- Initiate operations after quality assurance checks for proper cleaning
Cleanroom acceptable standards to check if your restarted cleanroom meets them.
- The room should meet all the ISO-14644 (including ISO-14644 part 3) specs for particles and air control.
- Airflow Test
- Air Pressure Differential Test
- Temperature Test
- Humidity Test
- Recovery Test
- Contamination Leak Test
- HEPA Filters (Annual Testing)
- EU Monitoring Guidance
- EU Annex 1 (2008) and MHRA Orange Guide (2014)
- ISO-14644 parts 1-12
- FDA Aseptic Processing Guide (2004)
- PDA TR #13 (2014)
- USP 37 <1116> (for Grades A, B,C,D)
- USP 37 <1115> (for Non-Sterile manufacturing)
*Viable and non-viable Contamination Sources:
*Difference between cleaning and disinfecting:
These are two distinct actions that should be performed in proper sequence to spic clean the room including engineering controls and other objects. Cleaning removes the ‘soil’ from the surface while disinfecting eliminates the vegetative organisms through the application of chemical germicide.
Disinfectant types
*Due to the non-specific nature of oxidizing agents, they present a greater risk of humans cleaning with them. Hence caution should be exercised.
Tools, Applications, and Sequence:
- Use microfiber wipes for removing some large debris
- Use mop heads to apply your detergents and disinfectants
- The mop head you use for ceilings and walls should be different than that used for floors.
- Though there are 2 mop and 3 mop bucket systems, to simplify things, apply the detergent and disinfectant to the mop head and wipe.
- Use bottles with spouts that facilitate a controlled pour rather than a spray bottle
- For wall cleaning, apply unidirectional overlapping downward strokes starting with the farthest end of the cleanest room and working your way out of the rooms.
‘Prevention is better than cure.’ Understanding where these events may occur and implementing a preventive plan and corrective action to the extent possible can help in minimizing the impact of worst case events on the environment, processes and production programs. To take a deep dive about restarting cleanrooms for production after shutdown, you may wish to sign up for the webinar ’Gaining and Re-Establishing Control of Your Cleanroom’. Mr. Polarine is a technical service manager at STERIS Corporation. He has been with STERIS Corporation for seventeen years.
You may also wish to browse through our list of webinars designed for life sciences personnel
.Compliance Trainings

Pregnancy in the Workplace: Strategies to Protect Your Organization from Pregnancy Discrimination Claims
By - Christopher W. Olmsted
On Demand Access Anytime
By - Christopher W. Olmsted
On Demand Access Anytime

How to Vet an IRB: Expose and Fix Problems Before They Threaten Your Trial
By - Madhavi Diwanji
On Demand Access Anytime
By - Madhavi Diwanji
On Demand Access Anytime

Compliance Standards
Best Sellers
- Add to Cart
- Add to Cart
- Add to Cart
- Add to Cart
- Add to Cart
- Add to Cart
- Add to Cart
- Add to Cart
-
By: Miles HutchinsonAdd to CartPrice: $249
- Add to Cart
- Add to Cart
- Add to Cart
- Add to Cart
- Add to Cart
- Add to Cart
-
San Francisco, CA | Aug 6-7, 2020
-
Virtual Seminar | Jul 16-17, 2020
-
Virtual Seminar | Jun 18-19, 2020
-
Los Angeles, CA | Aug 20-21, 2020
-
Virtual Seminar | Jul 16-17, 2020
-
Virtual Seminar | Jun 25-26, 2020
-
Virtual Seminar | Jun 10, 2020
-
Virtual Seminar | Jun 3-4, 2020
-
Virtual Seminar | Jul 6-7, 2020
-
San Francisco, CA | Oct 22-23, 2020
-
Virtual Seminar | Jul 9-10, 2020
-
Virtual Seminar | Jun 3-4, 2020
-
Virtual Seminar | June 3-4, 2020
-
Miami, FL | Jul 29-31, 2020
-
Virtual Seminar | Jun 17, 2020
-
Provider: ANSIAdd to CartPrice: $142
- Add to Cart
- Add to Cart
- Add to Cart
-
Provider: ANSIAdd to CartPrice: $120
-
Provider: ANSIAdd to CartPrice: $250
-
Provider: SEPTAdd to CartPrice: $299
- Add to Cart
-
Provider: Quality-Control-PlanAdd to CartPrice: $37
- Add to Cart
-
Provider: At-PQCAdd to CartPrice: $397
- Add to Cart
- Add to Cart
- Add to Cart
- Add to Cart
You Recently Viewed
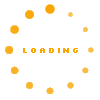