Your Shopping Cart
By using this site you agree to our use of cookies. Please refer to our privacy policy for more information. Close
Home
› Best Practices
Laboratory GMP Systems
- By: Nanda Subbarao, Ph.D
- Date: June 08, 2011
- Publisher: ComplianceOnline
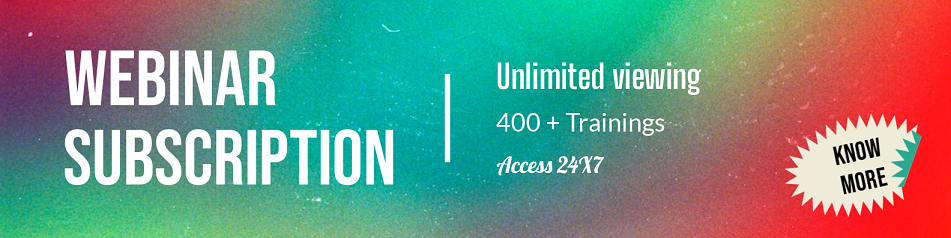
21 CFR Part 211 requires Pharmaceutical laboratories to comply with the cGMPs. Implementation of good cGMPs can also serve the business needs of the organization if implemented appropriately.
Documented scientific information is the primary business deliverable for R&D laboratories. The R&D laboratory management systems must therefore support generation of high quality information to decrease investment risks while moving the product to the next development phase. The information can be lost to the organization unless recorded promptly and archived in a manner which allows easy and rapid access. The importance of prompt documentation and witnessing is underscored by the fact that the date of the witness signature is the legal date on which the experiment is deemed to have been performed for IP legal purposes. The Drug Development laboratory differs from the academic lab in that the individual researcher is the owner and repository of the knowledge gained from the research. On the other hand in Pharmaceutical Development, it is the organization which owns and utilizes the Information. Organizations have relatively short memories compared to the individual researcher. Therefore Good Documentation Practices and Archival systems must be implemented in R&D laboratories even in early phases and become an important part of the GMP systems by Phase III and Commercial phases.
Facilities are designed for security of the personnel and equipment as well as the Intellectual Property. Facilities also have to satisfy local regulations for personnel and environmental safety and these elements must be included in the design of the lab space even from the earliest stages. During Phase I studies, Samples control could simply consist of a review of samples arranged in an orderly manner on shelves. As Manufacturing process development proceeds, the increase in the number and types of samples makes a formal sample management system necessary for effective operation of the laboratory. The same increase in sample load leads to increase in the number of analysts and amounts of reagent or solvent required. Therefore Personnel and Environmental Safety issues must be re-examined. The need for improving efficiency and sample turn around time drives the need for a well organized laboratory work space during Phase III and Commercial stage. A lab space, designed to facilitate easy cleaning, smooth sample and work flow and prevent sample mix ups leads to fewer errors and investigations and therefore improves efficiency. Such a lab space designed to prevent sample mix-ups is a GMP requirement.
The organizations investment in a Drug Development Project takes on an increasing risk if there is poor confidence in the performance, accuracy and precision of the testing equipment and software which generate the data which in turn form the basis of Project Decisions. Even in the Development Laboratory, a regularly scheduled preventive maintenance program is an easy way to improve reliability of laboratory equipment without significantly impacting the day-to-day work style of a scientist in the research laboratory. It is interesting to note that some DQ/IQ/OQ/PQ type activities are in reality performed for business reasons in well managed organizations even in early development phase. The organization can save Equipment Qualification resources by documenting these routinely performed activities. A fully documented lab equipment qualification program is a GMP requirement.
The success of a Drug Development program relies on competent laboratory personnel who are well supported by management. The appropriate hiring policy is therefore probably the first system that is implemented in a new organization, whether or not it is documented formally. Confidentiality Agreements and HR policy documents related to chemical safety and environmental safety are required from the earliest stages.
The competency and training of the employee need to be updated and maintained in the constantly evolving field of Pharmaceutical Development and cGMPs and the records/certificates of such training need to be added to the employee records. Such Employee Training files form the putative Records System for the formal Training Program during Phase I studies and which is made comprehensive and systematic as the Drug progresses through subsequent Phases.
Reagents and chemicals management systems in the research stage are rudimentary and at best may consist of a list of reagents and chemicals in the laboratory. A well run lab will have also implemented a system by which to avoid having multiple reagent bottles open and in use. A more formal, documented system will need to be implemented in time for Phase III studies to cope with the larger quantities of reagents and supplies due to larger sample through-put.
Dr. Nanda Subbarao, in partnership with ComplianceOnline, is conducting a full-day in-person seminar on Key GMP Systems in Biotech and Pharmaceutical Laboratories on Aug 01, at the Hampton Inn Philadelphia-International Airport, Philadelphia, PA.
For more information or to register for the event, please visit
http://www.complianceonline.com/ecommerce/control/seminar?product_id=80006SEM&channel=Article
Compliance Trainings

Pregnancy in the Workplace: Strategies to Protect Your Organization from Pregnancy Discrimination Claims
By - Christopher W. Olmsted
On Demand Access Anytime
By - Christopher W. Olmsted
On Demand Access Anytime

How to Vet an IRB: Expose and Fix Problems Before They Threaten Your Trial
By - Madhavi Diwanji
On Demand Access Anytime
By - Madhavi Diwanji
On Demand Access Anytime

Compliance Standards
Best Sellers
- Add to Cart
- Add to Cart
- Add to Cart
- Add to Cart
- Add to Cart
- Add to Cart
- Add to Cart
- Add to Cart
-
By: Miles HutchinsonAdd to CartPrice: $249
- Add to Cart
- Add to Cart
- Add to Cart
- Add to Cart
- Add to Cart
- Add to Cart
-
San Francisco, CA | Aug 6-7, 2020
-
Virtual Seminar | Jul 16-17, 2020
-
Virtual Seminar | Jun 18-19, 2020
-
Los Angeles, CA | Aug 20-21, 2020
-
Virtual Seminar | Jul 16-17, 2020
-
Virtual Seminar | Jun 25-26, 2020
-
Virtual Seminar | Jun 10, 2020
-
Virtual Seminar | Jun 3-4, 2020
-
Virtual Seminar | Jul 6-7, 2020
-
San Francisco, CA | Oct 22-23, 2020
-
Virtual Seminar | Jul 9-10, 2020
-
Virtual Seminar | Jun 3-4, 2020
-
Virtual Seminar | June 3-4, 2020
-
Miami, FL | Jul 29-31, 2020
-
Virtual Seminar | Jun 17, 2020
-
Provider: ANSIAdd to CartPrice: $142
- Add to Cart
- Add to Cart
- Add to Cart
-
Provider: ANSIAdd to CartPrice: $120
-
Provider: ANSIAdd to CartPrice: $250
-
Provider: SEPTAdd to CartPrice: $299
- Add to Cart
-
Provider: Quality-Control-PlanAdd to CartPrice: $37
- Add to Cart
-
Provider: At-PQCAdd to CartPrice: $397
- Add to Cart
- Add to Cart
- Add to Cart
- Add to Cart
You Recently Viewed
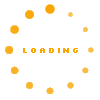