Your Shopping Cart
By using this site you agree to our use of cookies. Please refer to our privacy policy for more information. Close
Home
› Best Practices
Medical Device Quality System Regulations – A Brief Overview of FDA Requirements
- By: Staff Editor
- Date: September 16, 2011
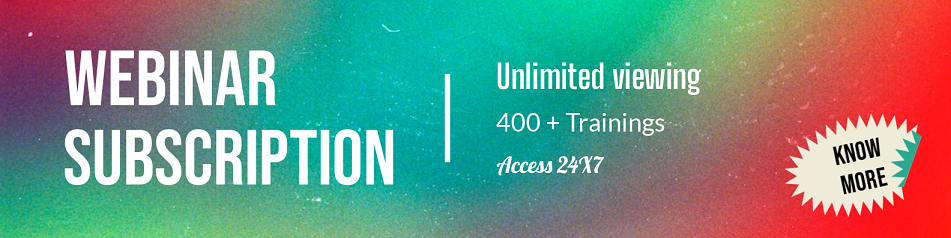
The FDA’s quality system regulatory requirements or Current Good Manufacturing Practices (cGMP) for medical devices have been detailed in federal regulation 21 CFR Part 820.
Applicability
The cGMP and quality system regulations apply to “the methods used in, and the facilities and controls used for, the design, manufacture, packaging, labeling, storage, installation, and servicing of all finished devices intended for human use.”
The requirements in Part 820 were formulated to ensure that devices are safe, effective and compliant with FDA regulations.
The regulatory requirements apply to the following:
- Manufacturers of finished medical devices
- Manufacturers, who engage in only some operations subject to the requirements in this part, and not in others, need only comply with those requirements that apply to those specific operations.
- Manufacturers of human cells, tissues, and cellular and tissue-based products (HCT/Ps) that are medical devices
Manufacturers of human blood and blood components are not subject to these requirements.
Definitions
Part 820 gives definitions of important terms that appear through the regulation such as:
Term
|
Meaning
|
Control number
|
Any distinctive symbols, such as a distinctive combination of letters or numbers, or both, from which the history of the manufacturing, packaging, labeling, and distribution of a unit, lot, or batch of finished devices can be determined
|
Design History File (DHF)
|
A compilation of records which describes the design history of a finished device.
|
Device History Record (DHR)
|
A compilation of records containing the production history of a finished device.
|
Device Master Record (DMR)
|
A compilation of records containing the procedures and specifications for a finished device.
|
Finished Device
|
Any device or accessory to any device that is suitable for use or capable of functioning, whether or not it is packaged, labeled, or sterilized.
|
Quality Policy
|
The overall intentions and direction of an organization with respect to quality, as established by management with executive responsibility.
|
Quality System
According to Part 820, each manufacturer should “establish and maintain a quality system that is appropriate for the specific medical device(s) designed or manufactured” and that fulfill the requirements detailed.
Need to improve your understanding of quality system requirements for medical devices? Then attend any of the
following ComplianceOnline webinars:
|
||
Quality System Requirements
This is divided into the following subsections and each is summarized below:
Management responsibility
|
Management is responsible for the following:
|
Quality audit
|
|
Personnel
|
|
Design Controls
Manufacturers should establish and maintain design control procedures for Class II and III devices and the following Class I devices:
- Devices automated with computer software
- Catheter, Tracheobronchial Suction
- Glove, Surgeon's
- Restraint, Protective
- System, Applicator, Radionuclide, Manual
- Source, Radionuclide Teletherapy
Procedures for the following design processes have to be established and maintained:
- Design and development planning
- Design input
- Design output
- Design review
- Design verification
- Design validation
- Design transfer
- Design changes
- Design history file
Document Controls
Manufacturers should establish and maintain proper document controls for the following procedures:
- Document approval and distribution:Manufacturers should designate individual to review documents for adequacy and approval prior to issuance
- Document changes: Changes to documents should be reviewed and approved by individuals in the same function or organization that performed the original review and approval, unless specifically designated otherwise
Purchasing Controls
Manufacturers should establish and maintain procedures to ensure that all purchased or otherwise received product and services conform to specified requirements. These controls should include:
- Evaluation of suppliers, contractors, and consultants
- Purchasing data
Identification and Traceability
- Manufacturers should establish and maintain procedures for identifying product during all stages of receipt, production, distribution, and installation to prevent mix-ups.
- Manufacturers of devices that are intended for surgical implant into the body or to support or sustain life should establish and maintain procedures for control number identification for each unit, lot, or batch of finished devices and where appropriate components. These have to be recorded in the DHR
Production and Process Controls
Manufacturers should develop, conduct, control, and monitor production processes to ensure that a device conforms to its specifications. These should cover:
- Production and process changes
- Environmental control
- Personnel
- Contamination control
- Buildings
- Equipment
- Manufacturing material
- Automated processes
Production and process controls also include:
- Inspection, measuring and test equipment and calibration
- Process validation
Acceptance Activities
Manufacturers should establish and maintain procedures for acceptance activities which include inspections, tests or other activities. Acceptance records should be properly maintained as part of the DHR.
Manufacturers should also identify the acceptance status of the product and this should be maintained throughout manufacturing, packaging, labeling, installation and servicing of the product.
Nonconforming Product
Control procedures for products that do not conform to specified requirements should be maintained and established by manufacturers. These should address the identification, documentation, evaluation, segregation, and disposition of nonconforming product.
Corrective and Preventive Action (CAPA)
Manufacturers should establish and maintain procedures for implementing CAPA and these should include requirements for:
- Analyzing processes, work operations, concessions, quality audit reports, quality records, service records, complaints, returned product, and other sources of quality data
- Investigating the cause of nonconformities relating to product, processes, and the quality system
- Identifying the actions needed to correct and prevent recurrence of nonconforming product and other quality problems
- Verifying or validating the corrective and preventive action to ensure that such action is effective and does not adversely affect the finished device
- Implementing and recording changes in methods and procedures needed to correct and prevent identified quality problems
- Ensuring that information related to quality problems or nonconforming product is disseminated to those directly responsible for assuring the quality of such product or the prevention of such problems
- Submitting relevant information on identified quality problems, as well as corrective and preventive actions, for management review
Labeling and Packaging Control
Procedures should be established and maintained for controlling the following labeling activities:
- Label integrity
- Labeling inspection
- Labeling storage
- Labeling operations
- Control number
Device packaging and shipping containers should be designed and constructed to protect the device from alteration or damage during the customary conditions of processing, storage, handling, and distribution.
Handling, storage, distribution and installation
Procedures should be established and maintained:
- To ensure that mixups, damage, deterioration, contamination, or other adverse effects to product do not occur during handling
- For the control of storage areas and stock rooms for product to prevent mixups, damage, deterioration, contamination, or other adverse effects
- For control and distribution of finished devices to ensure that only those devices approved for release are distributed
- Installation, inspections and tests
Records
All records should be reasonably accessible to responsible employees and FDA inspectors. These include the following
Device Master Record (DMR)
|
A manufacturer’s DMR should include:
|
Device History Record (DHR)
|
The DHR should include the following
|
Quality System Record (QSR)
|
The QSR should include:
|
Complaint Files
|
Procedures for receiving, reviewing, and evaluating complaints by a formally designated unit should be established and maintained
|
Services
- Instructions and procedures for performing and verifying that servicing meets specified requirements should be established and maintained
- Service reports should be analyzed with appropriate statistical methodology
- Service reports should be properly documented and should include:
- Name of device serviced
- Device identifications and control numbers used
- Date of service
- Individual servicing the device
- Service performed
- Test and inspection data
Statistical Techniques
- Procedures should be established and maintained for identifying valid statistical techniques required for establishing, controlling and verifying the acceptability of process capability and product characteristics
- Sampling plans should be written and based on a valid statistical rationale. Procedures should ensure that sampling methods are adequate and reviewed when changes occur. All these activities have to be documented
Additional Resources
Read the FDA’s Part 820, Quality System Regulation in full
Compliance Trainings

Pregnancy in the Workplace: Strategies to Protect Your Organization from Pregnancy Discrimination Claims
By - Christopher W. Olmsted
On Demand Access Anytime
By - Christopher W. Olmsted
On Demand Access Anytime

How to Vet an IRB: Expose and Fix Problems Before They Threaten Your Trial
By - Madhavi Diwanji
On Demand Access Anytime
By - Madhavi Diwanji
On Demand Access Anytime

Compliance Standards
Best Sellers
- Add to Cart
- Add to Cart
- Add to Cart
- Add to Cart
- Add to Cart
- Add to Cart
- Add to Cart
- Add to Cart
-
By: Miles HutchinsonAdd to CartPrice: $249
- Add to Cart
- Add to Cart
- Add to Cart
- Add to Cart
- Add to Cart
- Add to Cart
-
San Francisco, CA | Aug 6-7, 2020
-
Virtual Seminar | Jul 16-17, 2020
-
Virtual Seminar | Jun 18-19, 2020
-
Los Angeles, CA | Aug 20-21, 2020
-
Virtual Seminar | Jul 16-17, 2020
-
Virtual Seminar | Jun 25-26, 2020
-
Virtual Seminar | Jun 10, 2020
-
Virtual Seminar | Jun 3-4, 2020
-
Virtual Seminar | Jul 6-7, 2020
-
San Francisco, CA | Oct 22-23, 2020
-
Virtual Seminar | Jul 9-10, 2020
-
Virtual Seminar | Jun 3-4, 2020
-
Virtual Seminar | June 3-4, 2020
-
Miami, FL | Jul 29-31, 2020
-
Virtual Seminar | Jun 17, 2020
-
Provider: ANSIAdd to CartPrice: $142
- Add to Cart
- Add to Cart
- Add to Cart
-
Provider: ANSIAdd to CartPrice: $120
-
Provider: ANSIAdd to CartPrice: $250
-
Provider: SEPTAdd to CartPrice: $299
- Add to Cart
-
Provider: Quality-Control-PlanAdd to CartPrice: $37
- Add to Cart
-
Provider: At-PQCAdd to CartPrice: $397
- Add to Cart
- Add to Cart
- Add to Cart
- Add to Cart
You Recently Viewed
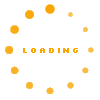