Your Shopping Cart
By using this site you agree to our use of cookies. Please refer to our privacy policy for more information. Close
Home
› Best Practices
Onboarding Training for New Hires in GMP Environment: Are You Complying?
- By: Staff Editor
- Date: September 12, 2017
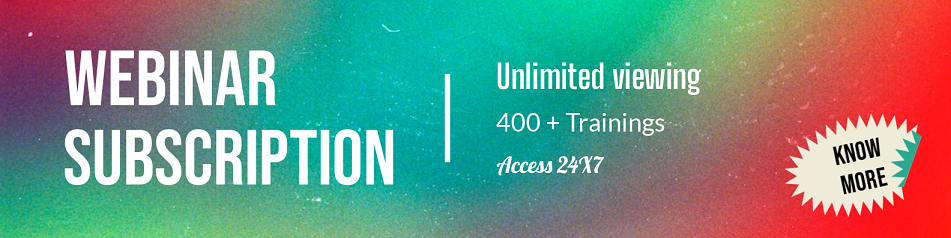
Onboarding Training for New Hires in GMP Environment: Are You Complying?
Onboarding training for the new hires in the GMP environment is a difficult task. Compliance requirements, quality concerns and work culture are all important considerations. Are contractors treated the same as long-term employees? Where does GMP training end and HR training begin? When can employees begin working? And all other barrage of questions need to be addressed.
Moreover, pharma companies need to have documented evidence that their employees are properly trained to perform their jobs to minimize errors on the job and avoid actions against them by regulatory agencies such as the U.S. Food and Drug Administration (FDA).
Additional Resources:
Webinar on Onboarding in a GMP Environment: Best Practices for Foundational Employee Success
GMP Training Requirements
Providing GMP training to the employees involved in manufacturing of FDA regulated products is a legal requirement. Title 21 Part 211.25(a) in the Code of Federal Regulations states that all employees must have a combination of education, training and experience in order to be qualified to complete their tasks.
GMP training is essential to ensure that professionals involved in the manufacturing, packing or holding of FDA regulated products understand the requirements of GMP regulations. GMP compliance training also educates employees on the best practices to comply with FDA good manufacturing practices.
Why is GMP Training Important?
Many Pharma companies have received Form 483s (i.e. observations) from the U.S FDA regarding noncompliance in the area of training. If this noncompliance is not addressed, the FDA can issue warning letters or place the company under Consent Decree, which can cost the company millions of dollars over an extended period of time, generate bad publicity and affect consumer confidence in the company's products. Some of the most commonly cited GMP violations in FDA warning letters include:
- Insufficient GMP training for employees
- Failure to establish written responsibilities and procedures for production and process controls, quality control units, stability testing, equipment cleaning and maintenance etc.
- Use of laboratory controls that have not been validated
- Deviations related to equipment maintenance, calibration and qualification
- Lack of documentation of cGMP activities e.g. changes made to integration parameters for the impurities test without appropriate documentation or justification
In one of the most recent cases, in August 2017, FDA warns Chinese Medical manufacturer for not providing any GMP related training to the employees who conduct or oversee manufacturing.
This clearly shows that identifying the training requirements for who has been hired, documenting their training completion, and following up to ensure that all new hires have completed training are some of the challenges faced by pharma companies.
Compliance Trainings

Pregnancy in the Workplace: Strategies to Protect Your Organization from Pregnancy Discrimination Claims
By - Christopher W. Olmsted
On Demand Access Anytime
By - Christopher W. Olmsted
On Demand Access Anytime

How to Vet an IRB: Expose and Fix Problems Before They Threaten Your Trial
By - Madhavi Diwanji
On Demand Access Anytime
By - Madhavi Diwanji
On Demand Access Anytime

Compliance Standards
Best Sellers
- Add to Cart
- Add to Cart
- Add to Cart
- Add to Cart
- Add to Cart
- Add to Cart
- Add to Cart
- Add to Cart
-
By: Miles HutchinsonAdd to CartPrice: $249
- Add to Cart
- Add to Cart
- Add to Cart
- Add to Cart
- Add to Cart
- Add to Cart
-
San Francisco, CA | Aug 6-7, 2020
-
Virtual Seminar | Jul 16-17, 2020
-
Virtual Seminar | Jun 18-19, 2020
-
Los Angeles, CA | Aug 20-21, 2020
-
Virtual Seminar | Jul 16-17, 2020
-
Virtual Seminar | Jun 25-26, 2020
-
Virtual Seminar | Jun 10, 2020
-
Virtual Seminar | Jun 3-4, 2020
-
Virtual Seminar | Jul 6-7, 2020
-
San Francisco, CA | Oct 22-23, 2020
-
Virtual Seminar | Jul 9-10, 2020
-
Virtual Seminar | Jun 3-4, 2020
-
Virtual Seminar | June 3-4, 2020
-
Miami, FL | Jul 29-31, 2020
-
Virtual Seminar | Jun 17, 2020
-
Provider: ANSIAdd to CartPrice: $142
- Add to Cart
- Add to Cart
- Add to Cart
-
Provider: ANSIAdd to CartPrice: $120
-
Provider: ANSIAdd to CartPrice: $250
-
Provider: SEPTAdd to CartPrice: $299
- Add to Cart
-
Provider: Quality-Control-PlanAdd to CartPrice: $37
- Add to Cart
-
Provider: At-PQCAdd to CartPrice: $397
- Add to Cart
- Add to Cart
- Add to Cart
- Add to Cart
You Recently Viewed
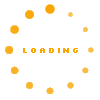